For detailed information, other images and documents, please select individual articles from the following table.
Multi-fibre structural adhesive reinforced with fibreglass
Transparent, universal and high-strength polyurethane adhesive with glass fibre reinforcement and excellent adhesion.
Register now and access more than 125,000 products






Variants
Register now and access more than 125,000 products
Call customer service: (23) 418-130
Prices for customers after login
Fibre-reinforced
- High-strength adhesive
- Thanks to the integrated glass fibre reinforcement, outstanding adhesive strength is achieved even with adhesive bonds under heavy loads.
- Highly impact-resistant bonding strength due to reinforcement fibres
Versatile applications and adheres to a wide variety of materials
- Compatible with natural stone
- Thin, transparent glue joint
- Semi-rigid adhesive with low foaming behaviour
- Can subsequently be powder-coated (30 minutes /+200 °C)
Hardens quickly
- Quick reaction time with high initial strength after approx. 20 minutes
- Enables you to continue working quickly
Proven adhesive properties
- Tested water resistance level D4 in accordance with EN 204
- Heat resistance according to EN 14257 (WATT 91)
Paste-like thixotropic adhesive (does not drip)
Can be sanded and painted over
Resistant to weathering and ageing
Silicone- and solvent-free
- Tested stress group D4 in accordance with DIN EN 204 by ift Rosenheim
- Tested heat resistance according to DIN EN 14257 (WATT 91) by ift Rosenheim
- French VOC emissions class A+
- The viscosity of 1C-PUR adhesives when processed at +15°C is approximately double that when used at +25°C.
- Sunlight discolours the adhesive but does not affect the adhesive strength!
- Bonding aluminium, copper, brass: Only on chemically pre-treated or coated surfaces: these materials cannot be permanently bonded in an age-resistant manner without appropriate pre-treatment of the bonding surfaces.
- Powder-coated workpieces should always be cleaned with cleaner type 60 (art. no.: 0892130030/0892130031); powder coatings with PTFE components cannot be reliably bonded without pre-treatment (e.g. plasma process).
- Pressing force: ≥ 0.015 N/mm² for surface bonding and ≥ 1 N/mm² for bonding solid wood to solid wood
- For bonding gap thicknesses ≥ 2.0 mm, the bonding, pressing and hardening times are considerably longer, bonding gap thicknesses ≥ 3 mm are not possible.
- If moisture is expected to have an impact, the bonding gaps/bonding surfaces must also be sealed/protected with a suitable sealing compound!
- When bonding metals to absorbent materials (e.g. wood, construction materials etc.), the moisture can be slowly transported through the bonding gap by the absorbent material onto the metal surface, where it can cause corrosion damage to the metal. The metallic bonding surface must therefore have suitable corrosion protection, e.g. paint or powder coating!
- When bonding different materials (with different expansion properties), the bonding gap dimensions must be adapted according to the long-term behaviour.
- The bonded workpieces should not be coated until after the adhesive is fully hardened; if they are coated too early, the formation of bubbles in the coating cannot be ruled out.
- Zinc-plated sheets should always be protected against the permanent influence of moisture. To prevent the formation of "white rust", any moisture that arises must be prevented from coming into contact with the bonding surface.
- In the production and processing of stainless steel, auxiliary materials such as wax, oils etc. are used. These materials usually cannot be simply wiped clean. It has been shown that after cleaning with solvents, grinding or (even better) sandblasting the surface, followed by repeated cleaning with solvents, delivers considerably better bonding results.
- Bonding larch: 1C-PUR adhesives must never be used for bonding larch surfaces in outdoor areas. The substance "arabinogalactan" which is contained in the wood, or forms within it, considerably weakens the bonding strength! No problems have been identified with PVAC and EPOXI adhesives.
- When bonding solid wood, the adhesive should preferably be applied to both bonding surfaces.
- For bonding solid wood in outdoor applications, suitable tests should be performed to determine the optimum permanent bond depending on the type of wood, weather intensity, surface protection and geometry of the bonding gap.
- The adhesive is mildly foaming and is therefore well suited to use on slightly uneven surfaces. The pressing time must be adjusted according to the thickness of the gluing joint.
- Skin-forming and joining times, as well as the respective pressing and processing times required, are influenced by criteria such as material, temperature, amount applied and air moisture, amongst others. As a result, they can only be precisely determined through independent tests. Corresponding safety margins for the specified reference values should be accounted for by the installer.
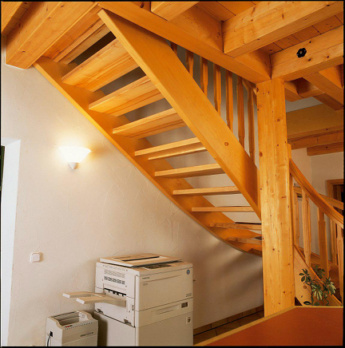
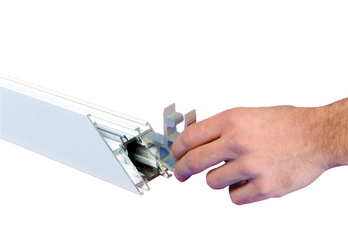
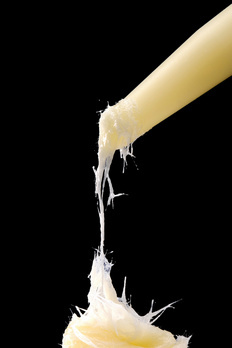
ASSEMBLY ADHESIVES | |||||
Multi high-strength adhesive 0893 100 110 | Multi-fibre adhesive 0893 100 115 | PUR Rapid 0892 100 102 | Assembly adhesive solvent-free 0893 100 100 | ||
Wood and wood materials | Wood (including MDF, chipboard) | ⎷ | ⎷ | ⎷ | ⎷ |
HPL laminated panels (Resopal, Ultrapas) | ⎷ | ⎷ | ⎷ | ⎷ | |
Decorative panels | ⎷5 | x | x | ⎷ | |
Cork | ⎷ | ⎷ | ⎷ | ⎷ | |
Stone and construction materials | Concrete | ⎷3 | ⎷3 | ⎷3 | ⎷3 |
Bituminous surfaces | - | - | - | - | |
Aerated concrete, gypsum, gypsum plasterboard | ⎷3 | ⎷3 | ⎷3 | ⎷3 | |
Synthetic stone (Corian, Varicor) | ⎷ | ⎷ | ⎷ | ⎷3 | |
Delicate natural stone (e.g. marble) | ⎷ | ⎷ | ⎷ | - | |
Stone | ⎷ | ⎷ | ⎷ | ⎷ | |
Cemented fibreboards | ⎷3 | - | - | ⎷3 | |
Other | Enamel | ⎷5 | - | ||
Glass | - | - | - | - | |
Fibreglass | ⎷ | ⎷ | ⎷ | - | |
Mirror | - | - | - | - | |
Porcelain, ceramic, tiles | ⎷ | ⎷ | ⎷ | - | |
Paper | ⎷ | ⎷ | ⎷ | ⎷ | |
Cardboard | ⎷ | ⎷ | ⎷ | ⎷ | |
Mesh | - | - | - | - | |
Leather | ⎷ | ⎷ | ⎷ | - | |
Metal | Aluminium | ⎷4,1 | ⎷4.1 | ⎷4.1 | ⎷1 |
Lead | - | - | - | - | |
Stainless steel | ⎷5 | x | x | ⎷1 | |
Copper | ⎷5,4,1 | x | x | ⎷ | |
Brass | ⎷5,4,1 | x | x | x | |
Steel/iron | ⎷5,4,1 | ⎷1 | ⎷1 | ⎷1 | |
Zinc | - | x | x | ⎷ | |
Plastics | ABS | ⎷4,2 | x | x | ⎷2 |
GRP | ⎷5 | x | x | ⎷2 | |
Rubber/neoprene | ⎷5 | x | x | - | |
Hard foams | ⎷ | ⎷ | ⎷ | ⎷2 | |
PE | - | - | - | - | |
PMMA | - | - | - | ⎷2 | |
Polyamide | ⎷ | - | - | - | |
Polycarbonate | ⎷ | - | - | ⎷2 | |
Polystyrene (not foam!) | - | - | - | - | |
PP | - | - | - | - | |
PTFE | - | - | - | - | |
PVC (not soft PVC!) | ⎷6 | x | - | ⎷2 | |
Silicone | - | - | - | - | |
Styrofoam | ⎷ | ⎷ | ⎷ | ⎷ | |
Painted surfaces | Painted surfaces (Two-part paints, stove enamels) Cathodic dip painted panels | ⎷5 | x | x | - |
1. Prime with Primer for Metal primer (art. no. 0890 100 66) 2. Prime with Primer for P/W/S (art. no. 0890 100 62) 3. Pre-treat with Deep-Penetrating Primer (art. no. 0890 545 10) 4. Pre-treat with Activating Cleaner (art. no. 0890 100 60) 5. Pre-treat with Cleaner Type 60 (art. no. 0892 130 030, 0892 130 031) 6. Pre-treat with Cleaner Type 10 (art. no. 0892 100 10) *Surface must not be moistened with lotus effect |
Optimisation table | ||
Surface/material | Optimisation steps* | Notes |
Anodised aluminium | 1. Activating Cleaner 2. AdhesionPlus metal | Notes |
Cathodic dip coating (E-coating) | Activating Cleaner | - |
Coil-coat coating | Activating Cleaner | – |
ABS | 1. Activating Cleaner 2. AdhesionPlus P/W/S | - |
GFRP (unsaturated polyester), gelcoat side or SMC | 1. Basic cleaning with cleaner type 60 2. Sand with "very fine" or grit 60-80 abrasive fleece and then vacuum. 3. Post-cleaning with cleaner type 60 | Adhesive surface must be protected against UV radiation (opaque cover). |
Hard PVC | Cleaner type 10 or type 60 | – |
Wood, plywood, MDF, wood products and cork | Dust | – |
HPL laminated panels (Resopal, Ultrapas) | 1. Cleaner Type 60 2. Varioprimer safe + easy | – |
Enamel, porcelain, ceramic, tiles | 1. Cleaner type 60 2. Varioprimer safe + easy | – |
Concrete, mineral mortar, plaster and cement fibre board | 1. Dust 2. Deep-penetrating primer | – |
Artificial stone (Corian, Varicor) | Cleaner type 60 | – |
Rubber/neoprene | Cleaner type 60 | - |
* Follow the corresponding sequence of the individual steps | ||
Aluminium (AlMg3, AlMgSi1) | 1. Basic cleaning with cleaner type 60 2. Sand lightly with "very fine" abrasive fleece 3. Post-cleaning with cleaner type 60 4. Activating Cleaner 5. AdhesionPlus metal | – |
Non-ferrous base metals (brass, copper, bronze etc.) | AdhesionPlus metal must be used. | |
Stainless steel (rustproof) | - | |
Steel (St 235 etc.) | In components susceptible to corrosion: 2-component PU or epoxy corrosion protection required! | |
Zinc-plated steel (hot-dip or galvanised) | Corrosion | |
Zinc | Formation of white rust when moisture is present | |
Powder coatings (PES, EP/PES) | Cleaner Type 60 | Preliminary testing is recommended for applications involving significant forces or a damp environment. |
2-component top-coat, water- or solvent-based (PUR, acrylic) | Varioprimer safe + easy | Due to the large number of paints available, this information is only a guide. Please perform preliminary tests where necessary. |
2-component primers, water- or solvent-based (PUR, acrylic, epoxy resin) | Varioprimer safe + easy | - |
For slot/pin gluing in wooden window construction, bonding corner angles in aluminium window and door construction, gluing board joints in wooden front doors, stairs, handrails, skirting boards, kitchen worktops, processing natural stone, metal window construction, windowsills, bonding round elbows and sandwich panels, general repair and assembly bonding. Ideally suited to the bonding of head blocks.
The base material must be clean, dry and free of grease. For pre-treatment, please refer to the optimisation table in the technical data sheet.
The bonded parts must be joined dry within the skin-forming time of approx. 7 minutes (approx. 3 minutes after wetting) and pressed for approx. 20 minutes with exactly fitting, tension-free bonded parts (with thick adhesive joints correspondingly longer) until the required functional strength is achieved. The adhesive is moisture-hardening.
For more information, please refer to the technical data sheet.
Select RAL-colour code
!! NOTE: On-screen visualisation of the colour differs from real colour shade!!